

Although what you are doing may be very simple, a very small mistake can really bugger things up.
Mazak m codes download code#
When you are happy with the code you can let the system look ahead again by turning look ahead back on. What we can then do is single block through the macro and check the calculations as we go. The system often will know the answer before you think it has seen the question. When we write a macro programme and we are testing it this look ahead is a real nightmare. Each move relies on the next for correct positioning. So this explains why the control looks ahead. They would all be the same Y position but in single block it stops ready for the next move three different places. As it moves up the left hand side it needs to know where its going in advance, moving round the outside in single block it would stop here. In order to machine the part without cutting into it the control needs to read in front. Below is a typical tool path where the tool is compensated to the left. Anyway CNC controls have to look ahead and here is why. When you test your macro you need to stop your control from looking ahead, put the blinkers on as it were. So having done all this you can lock out programme so no one can even see it. Also for parameter 82 if you put 33 into parameter 81 when you programme M33 the control will jump into programme You cannot pass arguments when you use an M code.īest not to argue then eh. Now you can do the same with your G code. It zeros the timer then runs it for the calculated time for each step.Īlias WTF? So for example if you put into parameter 92 when you programme a G it will jump to programme Just as if you had put M98 P or G65 P With a G code you can pass arguments to the programme a bit like G In G81 you tell it the depth and rapid point these are the Z and the R values.
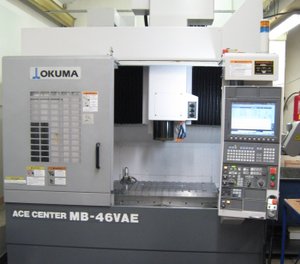
This will tell it how many times to go around the loop. It divides this speed by the speed increment that you give it. It goes on to calculate the difference between your start speed and your maximum speed. You also tell it the initial speed you want your spindle to start at from cold. You can tell it what RPM increase you want as a step. You tell it your maximum rpm you want to warm up to and the time you want the warm up to last. I must admit I often think that with Macro programming a little knowledge is a dangerous thing. Here are G-codes for Fanuc cnc control which are necessary for a….Tags : Mazak Training. We use cookies to ensure that you haveGthe Mazak best List Code experience on our website. M-Codes for both Upper unit and lower unit are given. Parameter Alarm M-Code List Mazatrol Matrix M We use cookies to ensure that you have the best experience on our website. M Overload detection time setting unit: 0.
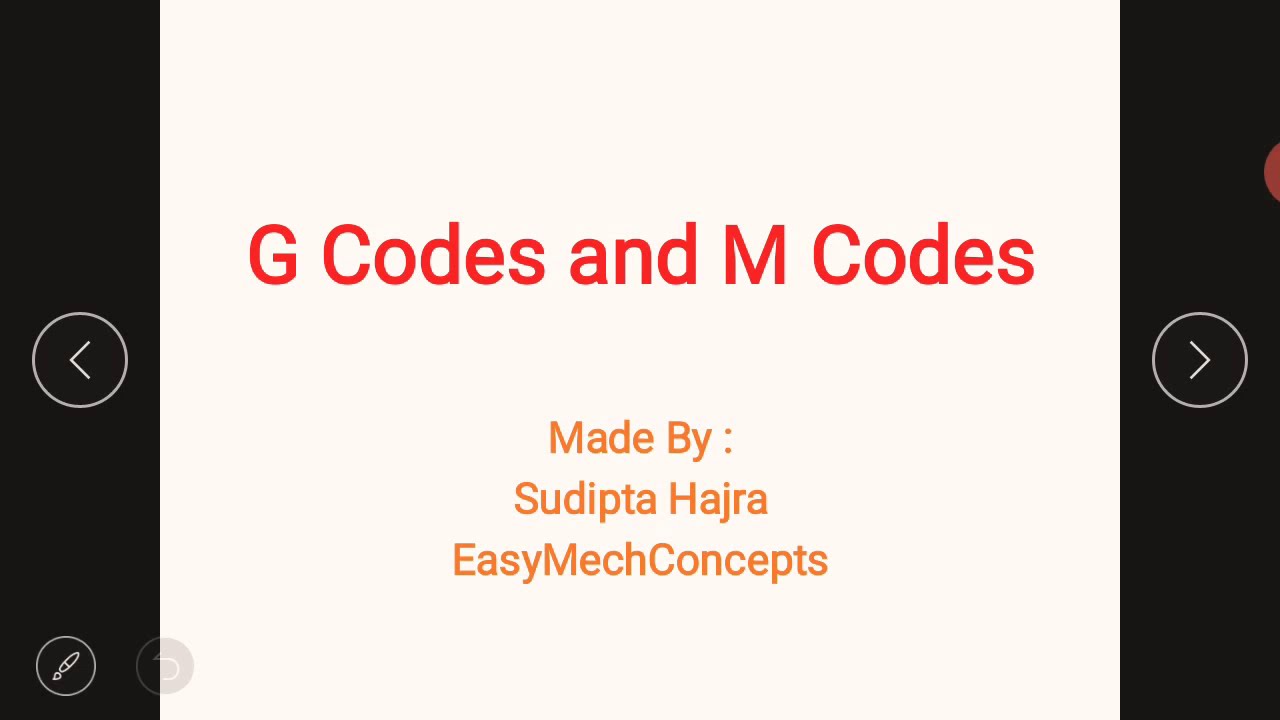
M Axis load detection, temporarily invalid. M Spindle speed arrival signal check, valid. M Spindle coil change fixed to high speed. M Milling head air blow We use cookies to ensure that you have the best experience on our website. M C-axis unclamp only unclamp by M M C-axis unclamp neglect mode cancel: M M Spindle speed check for interlocking the start of cutting. M C-axis clamp for milling We use cookies to ensure that you have the best experience on our website. M Workpiece rechucking for a piece delivered by robot. M Milling spindle through coolant OFF We use cookies to ensure that you have the best experience on our website. M Milling spindle through air blow ON Only for turning tools. M Workpiece measurement DIS start chuck barrier release. M87 Steady rest 1 clamp We use cookies to ensure that you have the best experience on our website. M75 Steady rest - milling head connection mode start. M67 C-axis brake for machining by G M74 Steady rest - milling head connection mode release. M45 Air coolant blow ON coolant stop: M M47 We use cookies to ensure that you have the best experience on our website. M19 Spindle orientation position for the robot to insert a workpiece. M12 Milling spindle mode cancel Turning mode selection. If you continue to use this site we assume that you accept this.
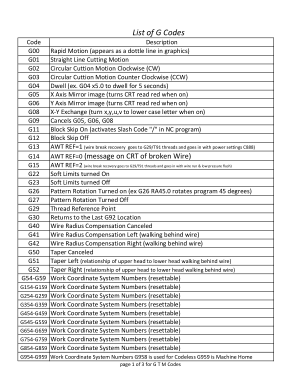
M07 have the best Chuck clamp on holding workpiece We use cookies to ensure that you experience our website.
